Проверка и оптимизация цепочки кинематической трансформации 5-ти осевого станка
- 9 июл 2025
- 10 мин
- 132
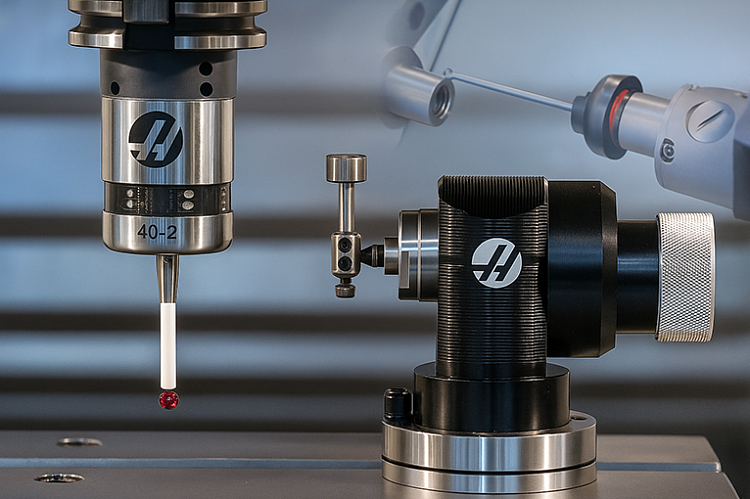
Так как цепочка кинематических трансформаций имеет свои уникальные размеры на каждом из станков в отдельности, перед пользователем встает задача измерения кинематических трансформаций на станке, под этим подразумевается определение расстояний от базовой точки станка до оси вращения.
Существуют ручные и автоматизированные технологии определения размеров трансформации, но все они несут единый смысл — это определение точной координаты физического центра оси вращения.
Сразу следует отметить, если на станке был удар или заменен узел, задействованный в расчете трансформации, например, стол или шпиндель, то необходимо перед настройкой кинематики провести проверку и правку геометрии на станке. Координата центра оси определяется в плоскости обработки, для оси A необходимо указать координаты центра Y и Z, для оси B необходимо указать координаты центра X и Z, для оси C необходимо указать координаты центра X и Y.
Циклы измерительного щупа позволяют производить измерение кинематики поворотных осей полностью автоматически. Из измеренных величин система управления вычисляет статическую точность поворотных осей. При этом программное обеспечение минимизирует ошибки, возникающие при развороте осей вращения, и автоматически сохраняет геометрию станка в конце процесса измерения.
С помощью функции обмера кинематики можно, измерять положение центра высокоточной сферы рабочем в пространстве станка под разными углами, тем самым рассчитать трансформации для 5-осевого преобразования (RTCP). Обмер выполняется таким образом, чтобы эталонная сфера измерялась с помощью измерительного щупа минимум в трех положениях на каждую круговую ось.
После обмера кинематики с помощью цикла, соответствующие переменные пользователя могут быть переписаны в таблицу кинематических трансформаций системы управления или автоматически активированы (все зависит от системы управления и цикла). В качестве альтернативы обмера с помощью цикла, кинематика может быть измерена вручную. Для обоих вариантов действительны одни и те же переменные пользователя.
Исходные данные для калибровки кинематики:
-
На станке должен быть откалиброванный измерительный щуп.
-
Эталонная калибровочная сфера, с графиком промера и точным размером.
-
Геометрия станка должна быть проверена согласно технологии завода изготовителя обрабатывающего центра.
-
Наличие цикла калибровки кинематики.
-
Примерные поворотные данные должны быть описаны в таблице трансформаций (с допуском в пару миллиметров).
-
Смещение нулевой точки должно быть деактивировано.
Порядок действий:
-
Удалить с стола зажимные устройства, заготовки и прочие предметы, которые могут привести к столкновению в процессе измерения кинематики.
-
Вызвать только что откалиброванный измерительный щуп в шпиндель инструмента.
-
Установить наклонно-поворотные оси в исходное положение 0°.
-
Смонтировать калибровочную сферу на стол станка таким образом, чтобы обеспечить безопасный разворот осей вокруг сферы на заданных пользователем углах. Для повышения точности измерений калибровочная сфера должна монтироваться как можно дальше от центра вращения круговой стола (см. рисунок 1) (для кинематики голова-голова, это не принципиально).
На рис. 1 слева изображена схема корректно выбранного положения калибровочной сферы относительно вращающейся оси станка: треугольник, который сформируется после измерения 3-х точек оси имеет наибольшую площадь. На том же рисунке справа изображена схема некорректно выбранного положения калибровочной сферы относительно вращающейся оси станка: треугольник, который сформируется после измерения 3-х точек оси имеет минимальную площадь, что приведет к неточным измерениям центра вращения оси.
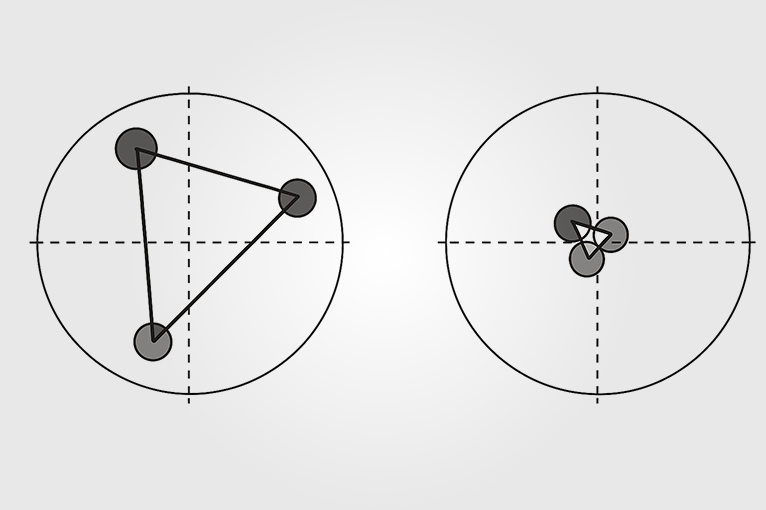
Точку южного полюса измерительного щупа необходимо расположить «на глаз», как можно точнее над центром сферы (рис. 2). Расстояние между кончиком измерительного щупа и калибровочной сферой должно быть приблизительно 5 мм.
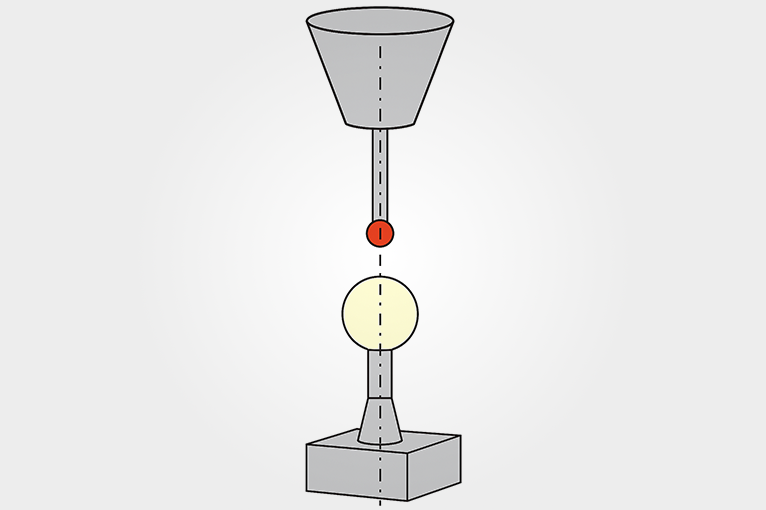
Далее необходимо ввести параметры цикла и отработать его. В качестве рекомендаций стоит упомянуть следующее:
-
Направление позиционирования круговых осей, для которых производится измерение, задается из углов, определенных в цикле. Начальный и конечный угол выбираются таким образом, чтобы система управления не измеряла одну и ту же точку дважды. Двойное измерение в точке (например, позиция измерения +90° и -270°) не имеет смысла.
-
При 0° автоматически производится эталонное измерение, если вы определили для измерения точку с углом 0°, система управления должна выдать сообщение об ошибке.
-
Вы можете выполнить грубую оптимизацию с меньшим числом точек измерения (2-3). Затем можно выполнить точную оптимизацию со средним числом точек измерения (рекомендуемое не менее 4). В идеале вы должны распределить точки измерения равномерно по диапазону наклона оси.
Следует всегда помнить, что высокая точность калибровки кинематики достигается за счет правильно настроенной геометрии станка, точно откалиброванного щупа, применения высокоточной сферы и проведения цикла калибровки столько раз, сколько потребуется для достижения отсутствия разницы в предыдущем и текущем измерении кинематики.

Благодарим Вас за выбор нашего технологического центра!
В ближайшее время наш менеджер свяжется с вами для согласования деталей.
Мы уже получили Вашу заявку на посещение нашего технологического центра.
В ближайшее время наш менеджер свяжется с вами для согласования деталей.
