RTCP - Контроль положения центра инструмента
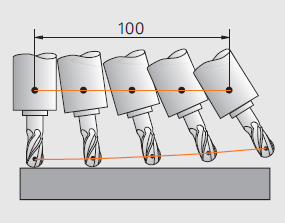
Современное автоматизированное производство невозможно представить без станков с числовым программным управлением и программных сред для автоматизированной подготовки управляющих программ. 40-50 лет назад пиком инженерной мысли были станки, поддерживающие объёмную 3-х осевую обработку, по большей части это было обусловлено ограничением вычислительной мощности аппаратной части системы управления. Сегодня научно-технический прогресс шагнул далеко вперед, и на рынке представлены многокоординатные обрабатывающие центры, поддерживающие непрерывную 5-ти осевую интерполяцию, главной целью которых является достижение максимально возможного качества выпускаемой продукции за меньшее количество установов и времени с улучшением точностных показателей и качества поверхностного слоя. Программно-математический аппарат систем управления обладает функционалом, позволяющим упростить работу со сложными трансформациями — это контроль положения центра инструмента.
Рисунок 1. Контроль положения центра инструмента
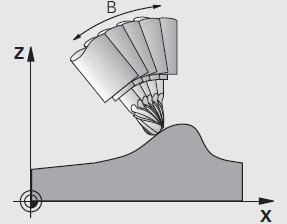
Одновременную или непрерывную обработку можно разделить на 2 типа по количеству задействованных осей в движении формообразования: на 4-х осевую и 5-ти осевую.
- 4-х осевая одновременная обработка представляет собой обработку с вращением компонентов, например кулачковые валы и другие детали машиностроения, в которых задействовано фрезерование по боковой поверхности цилиндра.
- 5-ти осевая одновременная обработка преимущественно применяется при изготовлении пресс-форм, обработке импеллеров или просто при создании эстетически привлекательных форм и дизайнов современных эргономичных устройств различных отраслей машиностроения.
При непрерывной обработке производится одновременное перемещение по четырём или пяти осям обрабатывающего центра, чтобы постоянно поддерживать требуемую ориентацию инструмента. Получившееся при этом смещение по линейным осям (при вершине инструмента) система управления должна определять и компенсировать. Для этого производителями систем управления была придумана функция контроля за положением южного полюса центра режущего инструмента — RTCP (Rotation Tool Control Point). Система управления в реальном времени начинает калькулировать положение кончика инструмента относительно формообразующей поверхности и выполнять все необходимые компенсации перемещения через поступательные оси, в том числе учитывая все кинематические особенности конкретного оборудования, на котором она применяется. Кинематика станка становится очень важным фактором для контроля за положением инструмента, так как невозможно идеально точно собрать механику станка в фиксированные кинематические «плечи», проще говоря, двух одинаковых станков не бывает. Для описания кинематических размерных цепочек в системе управления предусматривается таблица кинематических трансформаций, в которой задаются размерные цепочки трансформаций с точностью до микрометров — система управления берёт их в расчёт при слежении за положением инструмента.
Сразу хочется отметить, что у мировых производителей систем управления вызов функции контроля за положением инструмента называются по-разному, например G43.4 TCPM, G52 P2, TRAORI. Но по большей части они несут в себе единый смысл.
Причины применения одновременной обработки различны, такие как возможность обработки сложных форм деталей, например, фрезерование периферийной (боковой) поверхностью фрезы, улучшение качества поверхности сложной формы благодаря поддержанию постоянной скорости резания и постоянных условий резания.
Для большего понимания задач непрерывной 5-ти осевой обработки попробуем представить следующее: если начать делать построчное торцевое фрезерование сферической фрезой, то качество поверхностного слоя будет ужасным, так как у сферической фрезы на вершине режущая кромка будет ничтожно мала, а для обеспечения нормальной скорости резания, которая будет стремиться уйти на бесконечность, просто не хватит оборотов шпинделя. Но стоит наклонить фрезу на какой-то произвольный угол, как точка контакта изменится, и качество поверхностного слоя сразу начнёт улучшаться. Вместе с этим радиальные и осевые нагрузки на инструмент перераспределяются, что в итоге позволяет повысить режимы обработки и продлить срок службы режущего инструмента.
Смещение, получившееся в результате перемещения осей вращения, система управления компенсирует таким образом, чтобы вершина инструмента сохраняла своё положение относительно контура. Управляющие программы для обработки такого уровня сложности подготавливаются в среде САМ.
Рисунок 2. Перемещение без контроля положения центра инструмента

Если взглянуть на одновременно запрограммированные перемещение поступательной оси и поворотной без активации контроля за положением центра инструмента, то можно увидеть следующее:
G1 G90 X+100 B-30 F1000
Точка вращения поворотной оси движется вдоль запрограммированной траектории:
- Движение формообразования неправильное, как результат — получившийся контур неправильной формы;
- Расчётное значение подачи неправильное.
Рисунок 3. Перемещение с контролем положения центра инструмента
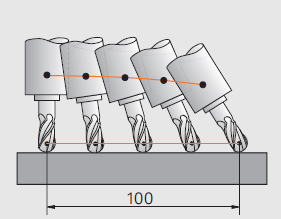
Но если запрограммировать одновременное перемещение поступательной оси и поворотной с функцией контроля за положением центра инструмента, то можно увидеть следующее:
G1 G90 X+100 B-30 F1000 «RTCP»
Сразу можно отметить, что точка центра инструмента движется вдоль формообразующей:
- Начальная и конечная позиции правильные;
- Контур правильный;
- Расчётное значение подачи правильное.
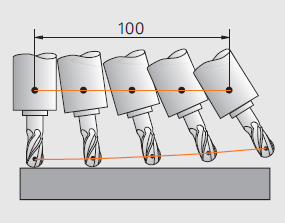
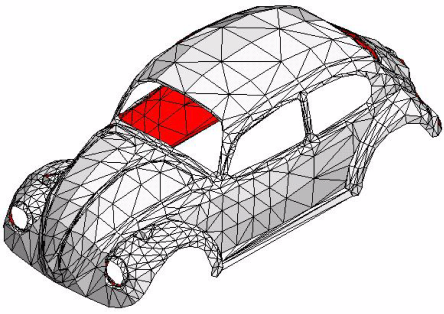
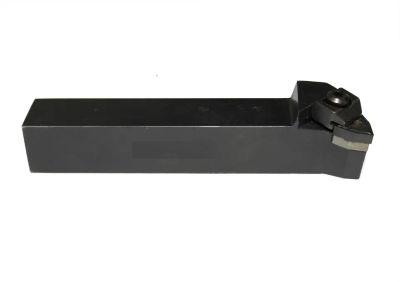

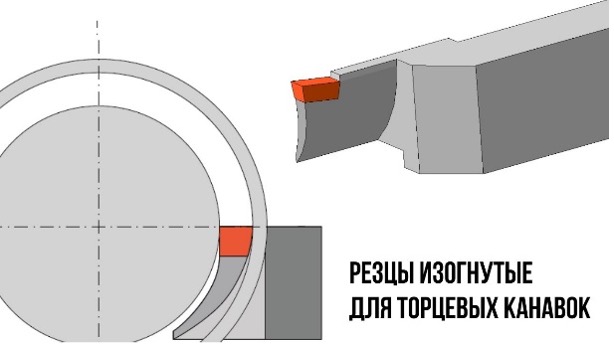