Как работает токарный резец: конструкция, история и современное применение
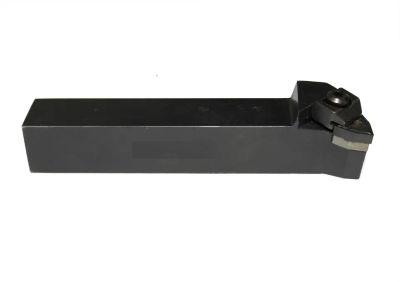
История появления резца, как орудия труда можно отнести к эпохе становления самого человечества. Благодаря этому инструменту удавалось механически воздействовать на форму изготавливаемых предметов. Современные резцы сильно отличаются от своих прародителей, но несмотря на это, спустя тысячелетия функция резца не изменилась.
С появлением первых станков ручные резцы сменились на машинные. Управляемый человеком станок с помощью резцов позволил изготавливать трудоёмкие детали, повторяющиеся по качеству и за более короткое время. Бурное развитие промышленности и экономики стало диктовать новые требования к оборудованию и в том числе к резцам. Время, затрачиваемое на изготовление, стало ключевым показателем. В погоне за временем принимались попытки увеличить скорость обработки, что приводило к быстрому износу токарных резцов. В свою очередь, замена изношенного резца на станке требовало дополнительного времени.
Эта проблема стала мотивацией в поиске новых инструментальных материалов, которые позволили бы увеличить срок службы инструмента. В прошлой статье мы рассказали, как Роберт Мушет внёс свой вклад в развитии металлургии. Так во второй половине 19 века была изобретена «Специальная сталь Роберта Мушет» которая стала прародителем быстрорежущей стали. Уже в конце 19 века режущий токарный инструмент имел более прочную основу из быстрорежущей стали, а в начале 20 века промышленность перешла на инструмент из твердого сплава.
Современный резец состоит из державки и режущей части. Классический токарный резец имеет державку с квадратным, прямоугольным или круглым сечением. Самые распространённые метрические квадратные державки имеют размеры: 12х12 мм, 16х16 мм, 20х20 мм, 25х25 мм и др. Прямоугольные – 32х25 мм, 40х25 мм и т. д. Круглые – 12 мм, 16 мм, 20мм и т. д. На рисунке 1 изображен токарный резец с державкой квадратного сечения.
Процесс резания выполняется таким образом: с момента контакта токарного резца и поверхности вращающейся заготовки происходит врезание резца. При дальнейшем относительном перемещении инструмента вдоль заготовки резец деформирует слой материала. А затем, этот деформированный слой, под воздействием резца и внутренних сил, скалывается и сдвигается передней поверхностью резца. Отделенный кусок материала называют стружкой. Этот процесс повторяется до тех пор, пока резец не покинет зону контакта.
На рисунке 2 представлены основные геометрические составляющие инструмента влияющие на характер резания.
Передняя поверхность является той самой поверхностью, по которой сходит стружка. Главная задняя поверхность обращена в сторону поверхности резания детали.
Главная режущая кромка – грань пересечения передней поверхности с главной задней поверхностью. Вспомогательная режущая кромка – это грань, образованная пересечением передней и вспомогательной задней поверхностей. Вершиной резца является точка пересечения главной и вспомогательной режущих кромок. Нужно понимать, что функции этих поверхностей зависят от взаимного расположения режущей кромки, детали и направления движения резца. Поэтому, чтобы не путаться в этих переменных параметрах были введены такие понятия как: плоскость резания, основная плоскость, главная секущая плоскость и вспомогательная плоскость. Плоскость резания – это плоскость, проходящая через главную режущую кромку касательно к поверхности резания. Основная плоскость параллельна направлению подач. Главная секущая плоскость перпендикулярна проекции главной режущей кромки на основную плоскость. Вспомогательная секущая плоскость перпендикулярна проекции вспомогательной режущей кромки на основную плоскость.
Давайте рассмотрим режущую часть токарного резца и выясним по какому принципу формируется процесс резания. На рисунке 3 представлена схематичная геометрия.
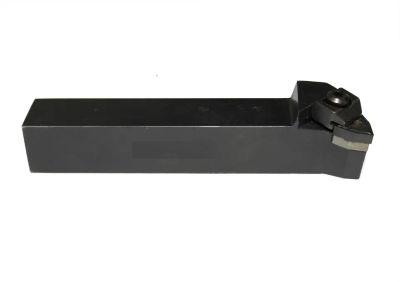
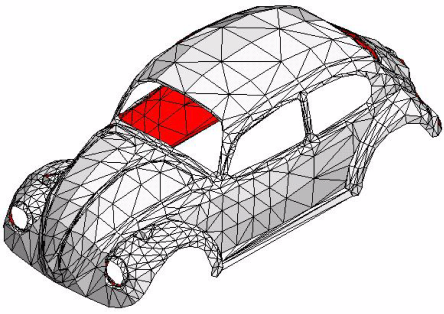

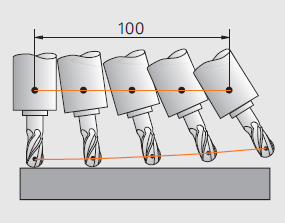
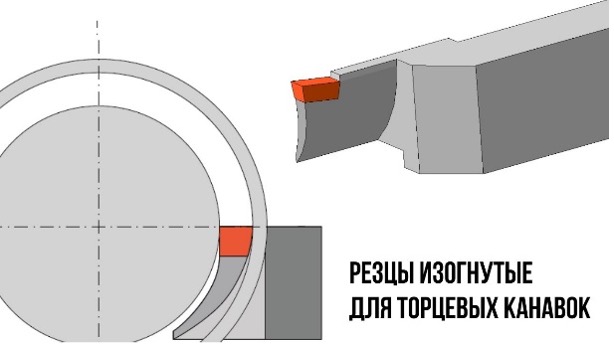